http://www.asyura2.com/15/hasan97/msg/574.html
Tweet |
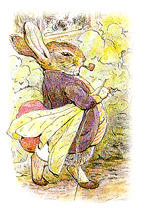
「技術経営――日本の強み・韓国の強み」
中小企業が技を持つ日本、企業格差が止まらない韓国
基盤産業が支える富士山型日本産業、セット事業リードの逆ピラミッド型韓国産業
2015年6月11日(木) 佐藤 登
日本のモノ作りが改めて見直されている。世界的に見て、きめ細かな匠の技が製品を引き立てることが取りあげられている。昨今における円安基調下での大企業輸出産業の好調ぶりもさることながら、個々のこだわりによる緻密で繊細な中小の技が、強みを放つケースは非常に多い。
新潟県・燕三条の世界に轟く金物類、大田区の町工場群の独自技術やオンリーワンなどがそれらの代表であろう。マスコミにも良く採り上げられる企業体は数多い。そのような存在感がある企業は日本のあちこちに点在している。日本ならではの匠の技術が認められ成長産業に発展している。
NHKの連続テレビ小説「まれ」でも登場する輪島塗もその1つで、その手の込みようは、文化そのものを発信している。漆の一般的な英語がJapanで定着していることも、文化そのものを意味していると言える。
一方、余談ではあるが、輪島の中でも輪島塗もどきが多いと聞く。それだけ、価値が高いから模倣品も出るのだろうが、日本の中で模倣品の存在は賛同できない。日本は常に、本物志向でグローバルに戦う必要があるし、戦えるからだ。
職人芸が商品を造る。これは、ユネスコ世界遺産になった「和食」文化にも相通じるものがある。素材の良さ、優れた加工、できあがった美しさ。美しいものは、おしなべて商品レベルは高いのが一般的だ。
地方に生きるブランド製造拠点
4月に秋田県横手市にある企業を訪問する機会を得た。ヴァルモードという企業である。横手市出身でもある筆者は、それまで、この企業の存在を知らなかった。訪問前に、凄い会社だという話は聞いていた。仏ラコステのスポーツシャツを中心にした縫製会社で、ラコステ本社が認める技術と品質とのことであった。
ラコステも世界各国に縫製工場を拠点としてもって展開してきたとのこと。なぜこの横手に、そのような世界に通じる技術や品質を持った製品が作られているのかという疑問を解決したく、訪問させていただいた。
世界の各拠点の製品をそれぞれ比較してみると、どうしても品質に差が生じ、品質の平準化が図れないとのことであった。結局は高品質なモノ作りができるかどうか。それでラコステは、品質の悪い製造拠点を段階的に封鎖していったとのこと。そして残った拠点の1つが、この横手市の企業との説明を受けた。
今では、日本製ラコステの90%以上が、この横手市での製品との事を知り驚いた。それだけ、競争力のある工場であることが立証され、ラコステ本社も十分に認めているとのことだった。では、どのような点が認められたのだろうか。
縫製も手作業で行えば、器用な日本人ならではの、きめ細かな製品を作ることは可能だ。しかし、それでは大量生産ができなくビジネスにならない。
縫製の主要作業はミシンが担う。既存のミシンの機能は設計された範囲での作業に留まる。しかし、2枚重ねでの縫製、縫い代が極めて狭くピンポイントでの縫製、ラコステのワニのマークの種類が豊富なため微妙に異なる縫製など、既存ミシンの機能だけでは到底対応できないものばかり。
そこからブレークスルーが起こる。そのような作業をスピーディにかつ精度よくできるように、ミシンにどのような動きをさせるかを考え、ミシンメーカーと協議し、ミシンの機能を作る。その機能によって、それまで難しかった縫製技術を可能にしている。そして安定した品質を実現している。
生地からの裁断工程のプロセスでも、いろいろな工夫が施されている。金型企業との製造プロセスの共同開発が、それを可能にしている。そういうプロセス開発が高品質の製品を作り上げているのである。
それが、他国や他企業ではできないことだとの自信にあふれた説明を聞くと、なるほど、これが差別化できるモノ作りの基本であると認識できる。
良い製品が実現できれば、それが標準となる。ラコステが製造を委託した企業といえども、そういう標準に追随できない企業は淘汰され、拠点は封鎖される。
企業規模の大小ではなく、モノ作りに込める想いや哲学、他ではできないことを実現する執着心、それがブランドを形作っていく。日本には、そのようなモノ作り精神の宝庫がたくさんある。
その貴重な技術力や品質づくりを埋没させることなく、世界に打って出ることのできるビジネスモデル作りは、まさに経営陣に課せられる命題である。
韓国の憂鬱
コラムのサブタイトルには、「セット事業リードの」と記したものの、韓国産業界には共通した弱みが浮き彫りになっている。
そこには大きく捕らえて3つの要素が浮き上がる。1つは、基礎研究分野が弱いこと、2つ目は素材・部材・装置産業分野が弱いこと、そして3つ目は中小企業の技や存在感が全くといってないことだ。
基礎研究分野は、根気強く時間をかけた取り組みが必要となる。その分、成果が出るまで時間を要し、短期間で評価されることは難しい。産業界では短期間での成果を求めがちだ。それは、サムスングループでも例外ではない。
従って、1〜2年単位で見えるテーマが優先される。その分、企業が大学や研究機関にその機能を委ねるケースが多い。あるいはまた、サムスングループのように、基礎研究部門をサムスン総合技術院という形で独立させた組織体系で、機能分担とマネジメントをしている大企業もある。
素材・部材の弱みの部分については、前大統領の李明博政権時代から取りざたされていた課題であった。「韓国のセット事業は強いが、素材や装置産業という基盤産業が脆弱だ。このままでは、韓国の産業界が将来的に成長発展していく道筋が見えない」と表現していたほど。
それだけに、韓国政府自らが主導する形で、多くの国家プロジェクトが発足した。2008年にスタートしたWPM(World Premier Material)もその1つで、2018年までの10年間で、将来に繋がる先端材料技術の実現に向けた研究を推進している。
このプロジェクトも発足から7年が経過して、残り3年となっている。顕著な成果は聞こえてこない。リチウムイオン電池の新素材も対象になってはいるが、業界の中で話題になっているものはいまだなさそうだ。
韓国内では国産の素材や部材調達を図るよう努力している。しかし、グローバル競争で戦えるほどの企業体が少ないのも事実である。そのような背景から、LGグループの中では、最大規模のケミカル事業を推進しているLG化学の存在は大きい。
同様に、サムスンもグループ内再編やM&Aを通じて、素材・部材事業を拡大しつつある。本来ならば、サムスングループやLGグループなどの韓国大手が素材・部材産業を育成する役割もあるはずだ。
しかし、それには時間がかかる。時間がかかるなら、グループ内での事業育成や拡大の方が早い。さらに、付加価値を作りやすいという考えも働き、そういう展開になりつつある。
装置産業もしかりである。少なくとも10年前には日本の装置産業界に負うところが大きかった。リチウムイオン電池の製造装置でも、日本からの輸入で韓国の電池業界が力を付けてきた経緯がある。
装置産業の基盤領域はセット事業とは異なり、きめ細かさやアイデアの創出、顧客ニーズにタイムリーに応える先取り開発が求められる。そういうニーズに対し、日本の企業は可及的速やかに応えようとする企業が多く、また力もある。
しかし、韓国内で仕事をしてきた筆者が見た装置産業界は、このような応答力は極めて低かった。標準的な製品を作ることには労を惜しまないが、いざ、難度の高い仕様を求められると、時間がかかるし、アイデアも必要になる。その地道な努力に傾注する企業が少ないし、力が不足しているということだ。
結果、どうなるか。サムスングループの場合、生産設備を外注で出すと上記のようなことになるのは分かっている。そうであるから、内部に生産技術部門を作り、そこを増強しつつ、内製化を進めてきた。
例えば、サムスンSDIのリチウムイオン電池の生産設備はその事例の1つである。2000年にモバイル用小型リチウムイオン電池の事業を始めてからしばらくは、装置メーカーへの外注、精度が要求される高機能装置は日本からの調達などで対応してきた。
しかし、生産工場での設備は歩留りや品質にも影響する。外注品であれば、それを改修したり開発したりで、多くの時間を必要とする。できればまだ良いが、できない場合もある。
そこで、サムスングループは生産技術領域に人材を投じ、開発力を増強してきた。モバイル用リチウムイオン電池は、ほとんどの生産工程の装置を内部設計している。車載用はモバイル用より歴史が浅い分、そして大型装置である分、難度は高いが、現在は車載用電池の生産設備の設計のほとんどは内部で行っている。
それによって、開発時間の短縮化、生産効率の向上、歩留りの向上など、恩恵を受けているところは少なからずある。日本の企業より、生産技術開発部門に資源を投じているのが現状だ。
韓国の格差社会を助長する中小企業の力不足
さらに、中小の企業体の力はと言えば、残念ながら力強さが聞こえてこない。日本の場合、先に述べたように、企業規模に拘らず、独自技術やオンリーワンはあちこちで聞こえる。
しかし、サムスンの韓国人に尋ねても、「韓国の中小で独自技術やオンリーワンというのは、まずないですね」という答えが返ってくるのだから確かなようだ。
これも、韓国の文化と相通じるところなのだろう。中小のレベルになると、請負的立場での対応でしかなく、自ら新たなアイデア発掘と言うスタンスでの行動がないのが原因である。
結果、中小はレベルが上がらず成長や発展もままならない。となると、財閥などの大企業と中小では大きな差が付く。大きな差が付くから、学生は財閥系などの大手に志願する。中小に人材が集まらない、結果として企業間で格差社会が形成される。
企業間格差が生じるから、大学生や大学院生の就職では大手に一極集中する。中でもサムスンへの志願者は国内最大だ。しかし、財閥大手といっても、採用人数には限りがある。
限りがあるから不合格者も多くなる。その結果、非正規職、または就職すらできない若者が続出する。韓国の若者の間にはびこる格差社会は、このような背景からも生じている。
今や、大学以上の卒業生の45%程度が正規社員としての採用、残りの55%は非正規職、または就職できない若者が家にこもるという社会構造は、韓国の憂鬱の一旦を担っている。
このように考えると、韓国の素材・部材・装置産業の競争力向上、中小でも独自技術などの魅力ある企業への変身が、韓国産業界の憂鬱を解消する答えのように映るが、果たしてどこまで開拓できるかは注目に値する。
このコラムについて
技術経営――日本の強み・韓国の強み
エレクトロニクス業界でのサムスンやLG、自動車業界での現代自動車など、グローバル市場において日本企業以上に影響力のある韓国企業が多く登場している。もともと独自技術が弱いと言われてきた韓国企業だが、今やハイテク製品の一部の技術開発をリードしている。では、日本の製造業は、このまま韓国の後塵を拝してしまうのか。日本の技術に優位性があるといっても、海外に積極的に目を向けスピード感と決断力に長けた経営体質を構築した韓国企業の長所を真摯に学ばないと、多くの分野で太刀打ちできないといったことも現実として起こりうる。本コラムでは、ホンダとサムスンSDIという日韓の大手メーカーに在籍し、それぞれの開発をリードした経験を持つ筆者が、両国の技術開発の強みを分析し、日本の技術陣に求められる姿勢を明らかにする。
http://business.nikkeibp.co.jp/article/opinion/20150609/284059/?ST=top
投稿コメント全ログ コメント即時配信 スレ建て依頼 削除コメント確認方法

すべてのページの引用、転載、リンクを許可します。確認メールは不要です。引用元リンクを表示してください。