http://www.asyura2.com/15/hasan95/msg/709.html
Tweet |
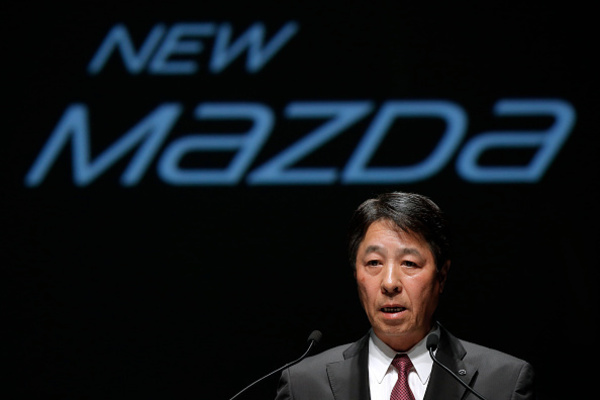
会見する子飼雅道社長 photo Getty Images
10年かけて実現したマツダ最高益。2006年に何を考え、何をしたのか?
http://gendai.ismedia.jp/articles/-/43067
2015年04月26日(日) 井上 久男「ニュースの深層」 現代ビジネス
マツダが24日に発表した2016年3月期の業績見通しは、売上高が前期比7%増の3兆2500億円、本業の儲けを示す営業利益は4%増の2100億円となる。営業利益は3期連続で過去最高を更新する見通し。当期純利益は12%減の1400億円となる見通しだが、3期連続好業績が続いたことで繰り越し欠損金がなくなったため、法人税率が24%から32%になることなどが響いた。配当は3倍の30円に引き上げる予定。
同日発表した2015年3月期決算でも、売上高は13%増の3兆339億円、営業利益は11%増の2029億円、当期純利益は17%増の1588億円で、営業利益、当期純利益ともに2年連続で過去最高を更新した。
■1ドル80円台でも収益が出る
マツダの復活の要因は、「商品力向上」に尽きる。世界のお客が欲しいと思うような斬新な車を、低コストで生産できるようになったからである。「モノ造り革新」と呼ばれる新たな手法によって開発した第一弾の「CX−5」以来、「アテンザ」、「アクセラ」、「デミオ」、「CX−3」とヒット車が続いて、いずれも高い評価を得て、販売増につなげている。円安効果も寄与しているが、マツダが採り入れた新たな開発手法では、1ドル=80円台の円高で輸出しても収益が出るという。
メーカーであれば、どの企業も「商品力向上」を目指すのは当たり前だが、実行が難しい。しかも、グローバルにビジネスを展開する自動車会社は、多様な価値観に対応しなければ、車は売れない。それはどういうことかと言うと、同じ車種であっても、国や地域によって嗜好や規制が違うため、設計やデザイン、部品などを変更しなければならない。これが設計部門などの負担となることで収益性が低下する。多品種少量生産に陥り、利益が出にくいということでもある。
しかし、こうした理屈は「作り手」の理論に過ぎない。消費者は、安い車、格好いい車、走りのいい車といった具合に様々な「価値」を求めてきて、それに応えていかなければ車は売れない。一方で、その「価値」に応えようとすれば、コスト増になるリスクもある。
マツダ復活の象徴はCX-3 photo Getty Images
マツダが取り組んだ「モノ造り革新」の狙いは、多様な価値観に対応しながらもコストを抑えた車を開発することにある。ハードの車というよりも、「価値」を作ることに主眼を置いた取り組みとも言える。
そのマツダの「価値」作りが成功した理由を考えてみたい。筆者は2008年ごろからこのマツダの取り組みを取材してきた。本コラムでも何回か断片的に紹介したが、改めて考えてみる。
■危機的状況の2006年に2015年の会社像を考えた
「モノ造り革新」のプロジェクトが始まったのは、2006年からだ。当時のマツダは経営危機に近い状態と言っても過言ではなかった。こうした中で、2015年にどんな会社になるべきかといった議論が社内でなされ、商品に織り込むユニット(エンジンや変速機やシャシーなど)の技術水準を2015年に世界一レベルにまで到達させるとの高い目標を定め、全車種を新しい技術に塗り替えてしまうことを決めた。
同時に2011年に発売する新車から新技術を適用することも決めた。これが「CX−5」である。しかし、マツダは資金など経営リソースが潤沢な会社ではない。これまでのように個別車種ごとに企画→開発→生産といったプロセスを踏んでいては予算や人手が足りなくなるという現実的な課題もあった。まして個別車種ごとの開発では開発期間も短縮できず、コスト削減にはつながらない。
これまでの日本の自動車会社では、車種ごとに開発責任者が存在し、その責任者がデザインや技術やコストなどの管理を総合的に束ね、開発が終わる頃にバトンタッチして次モデルの開発をゼロに近いところからスタートさせる「個別最適型」の開発が主流だった。部品などの共通化にしても前モデルの設計図の一部を流用するといった程度であった。
マツダは発想を大転換し、2011年〜15年に投入する新車を同時並行で開発していく仕事の仕組みに大きく変えた。このため、「モノ造り革新」は別名「一括企画」とも呼ばれる。
2015年時点でも通用する高い水準の技術が求められる一方で、コストも安くしなければならないため、これまでの常識を否定するような車造りが求められた。目に見えるモノを共通化するというよりも、思考プロセスや設計構想、それを具現化する生産プロセスを共通にしなければならなかった。
マツダの場合、限られたリソースの中での挑戦というのもポイントで、その象徴が開発投資のかかるハイブリッドの自社開発は捨てて、ガソリンエンジンやディーゼルエンジンといった内燃機関の進化にリソースを集中させたことも奏功した。「スカイアクティブエンジン」の誕生は、その活動の結晶である。
経営が悪化している中、短期的な対応だけに終始するのではなく、生き残りをかけて長期的な視点で商品力向上を目指したのである。こうした取り組みというか発想に、日本の製造業が学ぶべき点が多々ある、と筆者は感じる。
■世界の製造業のお手本
これまで日本の製造業は一般的に、工場での業務効率を高めることでコスト削減を実施し、利益を確保する傾向が強かったため、いくら開発側が斬新なデザインなどの新商品を提案しても、生産ライン(生産技術)が制約となって、商品力を犠牲にするケースが多く見られた。単純化して言うと、工場側が「こんな新しいデザインや設計の車は、今の製造ラインで流せない」と言えば、開発側はそれを呑んで設計変更をしなければならなかったわけで、これが、商品力を犠牲にするという意味である。
しかし、マツダの場合は、開発の初期段階から、設計と生産技術が一体となってエンジンや車体などの開発を行うことで、開発陣が造りたい車を造れるようにもなった。
同時に製造現場は「フレキシブル生産」体制を導入した。その特長の一つに汎用機の活用が挙げられる。マツダ本社工場でエンジンのシリンダーブロックを製造するラインでは、1工程当たり14台の汎用マシニングセンター(MC)が並ぶ。「モノ造り革新」の前までは専用機で対応していたのを改めた。専用機は大量生産には適しているが、変種変量には弱いからだ。汎用MCだと1台が生産を止めても他の13台は動いているが、専用機は1工程が止まると全体の流れも停止してしまう。しかも刃具や治具交換のために一旦止めると専用機は再プログラムする段取り替えにも時間を要する。
汎用MCの積極活用によって、機械を停止することなく、1ラインで多様な製品を生産できるように変えた。発想を変え、機械が動いている時間を「付加価値」とみなす方式に切り替えたのである。この結果、13種類のエンジンを一つのラインで流せて、専用機時代には45工程あったのが4工程にまで激減させることに成功した。設備投資額も従来比で70%削減できたという。
こうしたマツダの取り組みは、世界の自動車メーカーのベンチマークの対象となっている。トヨタが今年中に発売する新型プリウスから、新しい設計・生産手法「トヨタ・ニューグローバル・アーキテクチャー(TNGA)」が導入されるが、その発想や手法はマツダの「モノ造り革新」と似ている部分がかなりある。世界のトヨタもマツダの取り組みをお手本にしているということである。
今後、マツダは円安でも海外生産を強化する。どのメーカーも同じだが、自動車は消費地に近いところで生産するのが原則である。特にマツダの場合、メキシコ工場を起点に北米や南米、欧州市場の攻略を狙うため、メキシコ工場の生産性向上などが課題になる。マツダを再生させた「モノ造り革新」がグローバルに根付くかが、今後も持続的成長を維持できるかのカギとなるだろう。
投稿コメント全ログ コメント即時配信 スレ建て依頼 削除コメント確認方法

すべてのページの引用、転載、リンクを許可します。確認メールは不要です。引用元リンクを表示してください。