http://www.asyura2.com/14/hasan87/msg/367.html
Tweet |
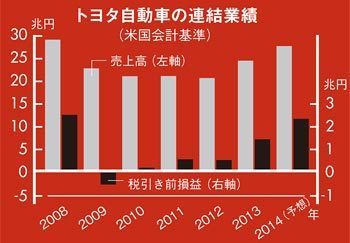
検証! トヨタ自動車の復活は本物か【1】
http://zasshi.news.yahoo.co.jp/article?a=20140428-00012421-president-bus_all
プレジデント 4月28日(月)13時45分配信
「トヨタショック」を乗り越え、トヨタ自動車は業績を回復させ、復活してきた。果たして、このトヨタの復活は本物なのか。気鋭のジャーナリストが徹底検証する。
■トヨタショックからDNA復活の道のり
トヨタ自動車は13年11月6日、2014年3月期決算の通期業績で売上高が前期比13.3%増の25兆円、本業の儲けを示す営業利益が66.6%増の2兆2000億円、当期純利益が73.6%増の1兆6700億円になる見通しだと発表した。
対外的に公表したこの数値は、実はかなり堅い見通しである。あるトヨタ幹部は「営業利益は08年3月期の過去最高益(2兆4372億円)を更新するのは間違いないだろう」と見る。トヨタの収益力は08年9月のリーマンショック前に戻りつつあると言ってもいいだろう。
同時に発表した確定値の14年3月期中間決算も当然ながら好業績だった。売上高は前年同期比14.9%増の12兆5374億円、営業利益は81.0%増の1兆2554億円、当期純利益は82.5%増の1兆6億円だ。営業利益率も10%の大台に乗り、ホンダ(6.2%)や日産自動車(5.1%)を大きく引き離した。
今回のトヨタ決算の大きな特徴は、グローバルでの販売台数は落ちたのに売上高と利益がともに大幅増になった点にある。トラック専業の4社を除く日本の自動車メーカー7社(トヨタ、ホンダ、日産、スズキ、マツダ、富士重工業、三菱自動車)の中で、連結販売台数が減っても増益となったのはトヨタだけだ。
そのトヨタの販売台数は、1.1%マイナスの約447万台で、エコカー減税の反動で日本、経済減速の影響で東南アジアがそれぞれ落ち込んだものの、高価な車が売れる北米で販売を増やしたことで売上高を伸ばした。営業利益については地域別利益で日本が過去最高となる前期比3.3倍の8300億円を記録した点を特筆すべきだろう。増益分のほとんどは国内で稼ぎ出していることになる。3年前までは日本は営業赤字だったのに、急激に盛り返した。
その理由は、円安による輸出車の利益率上昇もさることながら、トヨタの「お家芸」である原価改善努力をこつこつと積み上げたことや、生産が増えなくても利益を出せる体質を構築してきたことが大きい。こうした特徴は、トヨタ的経営が本来持つ強みであり、トヨタのDNAと言っても過言ではない。それが2000年代に入って北米を中心に膨張、兵站が伸び切ってしまった中で、トヨタのDNAが忘れ去られている面がある。今回の好決算は、いわば「先祖返り」してトヨタ流の経営に忠実に取り組んだ成果とも言えよう。DNA復活でもある。
その地道な取り組みとはどのようなものかを紹介する前に、リーマンショック後に襲いかかったトヨタの艱難辛苦の道のりを振り返る。なぜなら、リーマンショック前の膨張経営を反省した上に今の取り組みがあるからである。
「トヨタショック」が始まったと言われたのがちょうど5年前の08年11月6日だった。この日トヨタは09年3月期決算の通期業績見通しの下方修正を発表。海外の子会社などの利益を含まない単独決算で輸出の不振などから本業の儲けを示す営業損益が下半期に赤字に転落するデータを開示した。トヨタが戦後初の営業赤字に陥ることになったため、そのニュースは新聞紙上をにぎわした。ただし、その時点で連結決算では通期で6000億円の営業黒字を確保する見込みだった。
ところが、それから2カ月もたたない12月22日、渡辺捷昭社長(当時)が記者会見、通期でも1500億円の営業赤字になる見通しを発表。わずかの間に7500億円もの利益が吹っ飛んだ。販売台数も5月の期初予想の906万台から12月22日時点では754万台にまで落とした。一気に152万台減少したことになる。一般的に一つの自動車工場で年間に約30万台造ることから考えると、工場5カ所分の販売量が消えたことになる。特に「レクサス」や大型ピックアップトラック「タンドラ」など高価格帯の車が売れていたドル箱の北米市場が急速に縮小したことが収益悪化に拍車をかけた。
■業績悪化の裏に「内なる敵」の存在
08年9月にリーマンショックがあったとはいえ、トヨタの業績悪化の本質的な理由は「内なる敵」に敗れてしまったことにある。単に「リーマンショックの影響」と一言では片づけられない。社内で無防備な収益追求主義が第一となり、儲けは顧客に商品やサービスが評価された後からついてくるという発想に欠け、安くて良い商品をいかにつくるか、あるいは商品づくりの前にいかに人材育成に取り組むかといった、トヨタが最も大事にしてきたことが失われ始めていたのである。
その象徴的な事例をいくつか挙げると次のようなことがある。米国で売れば儲かったから米国仕様でほとんどの車を設計したため、「カローラ」などトヨタを代表する大衆車の大型化・高級化が進んだ。この結果、「カローラ」は米国以外ではあまり売れなくなった。この大型・高級化路線を象徴するのが、米国専用モデルの大型ピックアップトラック「タンドラ」だ。この「タンドラ」を、巨額投資で新設した米テキサス工場で製造し始めた。トヨタは売れ行きに変動があっても生産ラインの稼働率が極力変わらないように一つのラインで複数の車を生産する「混流生産」を得意としてきたが、テキサス工場は「タンドラ」の専用工場として建設された。これまでのトヨタの中では異例中の異例の工場だった。
大型ピックアップトラックを専用工場で大量生産することで利益を増やしたものの、大きなリスクも孕んでいた。リーマンショックで「タンドラ」の販売が落ち込み出すと、稼働率が一気に落ちて揚げ句には3カ月近い全面操業停止に追い込まれた。自動車産業は多くの社員を抱えて設備も高額・巨大で固定費が高い産業であるため、操業率が落ちると、動かない設備はキャッシュを生まず、しかも働かない社員に給料を払うことにもなり、一瞬にして赤字に転落する。トヨタも例外ではなかった。
そもそも「タンドラ」は「原価企画の段階から赤字だった」と言われている。100%近い部品が専用で開発された。ここでも「お家芸」だった他車種で使った部品を転用し、開発コストを極力抑える発想が消え失せていた。当時の社内には「原価が高いのなら値上げすればいい」といった傲慢な意見もあった。完全な驕りである。
トヨタで驕りが生まれた背景には、「グローバル・プロフィット・マネジメント(GPM)」という指標の導入が大きな原因と見られている。機関投資家向けに説明した利益目標を達成するために地域ごとに利益目標が課せられるようになった。それまでのトヨタでは現場からの積み上げ方式で利益をはじき出してきたのに、本社が机上で決めた数値で「はい、これをやってください」といった手法に切り替わったのだ。
「GPM」によって利益計画がぴったりと決まっているため、経営環境が変わって新しい目標や課題が生まれても、トヨタはその対応に柔軟に取り組めない硬直的な組織になっていったのである。
こうした危機的局面の中の09年1月、トヨタは豊田章男氏の社長昇格を発表した。記者会見で豊田副社長は「あえて言うなら現場に一番近い社長でいたいと思っています」などと抱負を語った。ところが社長就任後、追い討ちをかけるかのように、09年秋には米国でのリコール問題、11年3月の東日本大震災、同年9月のタイ大洪水といった具合にアクシデントが立て続けに発生してトヨタの業績は一向に回復しなかった。
しかし、豊田氏はめげずに環境の変化に素早く対応し、小回りが利くものづくり体制の構築を進めた。同時に社内外に「良品廉価」という考えを喧伝し、下請け企業や販売店も含めてオールトヨタでいい車を造っていくことだけに注力する組織風土づくりを目指した。時に豊田氏はこうした取り組みを総称して「もっと笑顔で仕事をしましょう」とも呼びかけた。
■「断トツライン」と「設計革命」
地道な活動であるものづくり面での改革で大きな取り組みは2つある。一つは「断トツライン」と呼ばれる生産性を極めて高めた現場づくりだ。2013年秋にトヨタの主力工場のひとつ高岡工場に導入された。すでに「断トツライン」の源流は、国内最新工場である子会社のトヨタ自動車東日本の宮城大衡工場(宮城県大衡村)にある。筆者も13年6月に取材に出かけた。あらゆる点に知恵を注ぎ込んだ工場だ。たとえば、車体をハンガーで吊るして流す方式をやめて、レールの上を流れる「自立式」に替えたことで、屋根を低く、かつ建屋の強度を落とすことができて投資コストを5割カットした。また需給や車種の変動に応じて生産ラインの長さを瞬時に短くできるラインにしたことで製造コストも激減、1ドル=80円台半ばでも国内生産で利益が出る体制を築いた。しかも、これまでは一つの工場で最低年産20万台ないと利益が出にくかった体質を、「断トツライン」の導入によって年産10万台でも利益が出るように改めた。
この生産量が落ちても利益が出る体質づくりは海外でも進んでいる。トヨタタイのバンポー工場で製造したピックアップトラックやSUV は世界100カ国に輸出されている。バンポー工場では、固定費という考え方はなく、すべての仕事にかかるコストを変動費として計算して事業環境の変化に強い工場運営にしている。この結果、稼働率が40%にまで低下しても利益が出る体質になった。非常に生産性が高い工場でもあり、何秒で1台を生産できるかを示すタクトタイムはバンポーでは56秒。日本のトヨタの工場よりもタクトタイムは早いときがある。工場内も徹底的に整理整頓が行き届き、トヨタ生産方式(TPS)の思想を徹底的に採り入れた工場運営をしている。
こうした取り組みなどによって、トヨタはリーマンショック後、総額1兆5000億円の原価低減効果を生み出し、同じく総額で1兆2000億円あった円高による為替差損を穴埋めした。リーマンショックの前に過剰設備・水膨れ体質になって、需要の変動が起きると一気に赤字に転落したことを反省しての取り組みとも言えるだろう。
もう一つの柱は「トヨタ・ニュー・グローバル・アーキテクチャー(TNGA)」と呼ばれる「設計革命」だ。開発や生産技術のエンジニアが仕事の進め方をゼロから見直すことに取り組んでおり、「仕事革命」でもある。この取り組みは、トヨタが完全復活し、その後も持続的に健全な成長を遂げていくために必要な戦略とも言える。
TNGAではまず、トヨタの総生産台数の50%に相当する前輪駆動(FF)系プラットホームから設計革新に取り組む。「ヴィッツ」「プリウス」「カムリ」の3つのプラットホームに集約し、この3つをベースに複数の車種を開発し、部品や構造(レイアウト)の共通化などを進める。その第一弾は15年発売予定の4代目「プリウス」となる見込みだ。
TNGAの取り組みで大きなポイントとなるのは、デザイン・設計の源流段階から10年程度先までの商品を同時開発し、一気に共通化を進めていくことである。そして、デザインや設計を大きく変えても、製造現場がこれに対応できなければ「絵に描いた餅」に終わってしまうため、デザイン、開発、生産、調達といった各機能が源流段階から同時に車造りに取り組む。非常にコンカレントな取り組みであることが特徴の一つだ。こうした仕事の進め方を加速させようと、トヨタは今春、開発と生産技術が同居して大部屋方式で車造りに取り組む開発棟を建設した。
また、これまでのトヨタの開発スタイルは、プラットホームを共有化していながらも、車種ごとにチーフエンジニア(CE)が存在しているために、搭載する部品は個別に設計したり、後発車種では設計を大幅に見直したりするなど、個別最適の設計をしているのが実態だった。これを見直してプラットホームが同じであれば、部品や構造(レイアウト)を徹底して共通化する。たとえば、同じプラットホームでも、エンジンルーム内のレイアウトは違うケースがあったが、今後は統一化していく。これにより部品や取り付け作業の共通化も進み、効率性が増すことになる。
車種ごとにいたCEは、車種群担当のCEとして大括りにして、車種群の開発に責任を持たせる。さらにCEは個別の車種開発が終われば人事異動で交代していたが、こうした習慣も改め、CEが継続的に商品群を改良していく仕事の進め方を導入する。長期的視点で商品開発に取り組み、部品や構造の共通化の推進を確実にしていくための組織改正である。
ジャーナリスト 井上久男=文

すべてのページの引用、転載、リンクを許可します。確認メールは不要です。引用元リンクを表示してください。